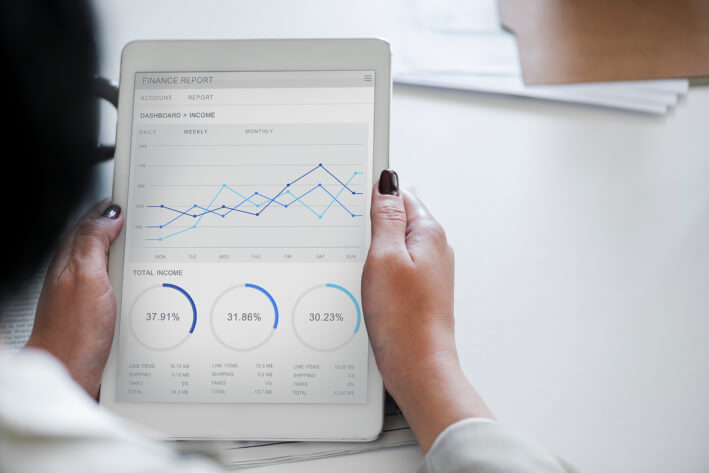
The Effect of Demand Planning and Forecasting
A lot of businesses hugely rely on demand planning and forecasting for their operations. They look at all these forecasting reports to lessen the risks they take out of their decisions. There are also demand forecasting tools such as statistics, software, and apps they can use for a more accurate demand planning and forecasting. There are even some companies who assemble teams who work exclusively on this particular task aside from their regular employees.In our company, we provide demand planning and forecasting services for our clients in support of the products they launch and continue to manufacture. We make sure the objectives are modified according to the outcome of our demand planning and forecasting. For example, if our client is planning to manufacture 100,000 units of their latest product but the forecast suggests demand is low for the product. We will ask our client to modify the numbers and only manufacture 30,000 to 50,000 units to avoid potential loss. This is the part where the marketing department will do their magic and promote the product to further increase the demand later.
As you can see, demand planning and forecasting do not only impact the manufacturing process but also play a huge role to cost estimation and other financial aspects of an organization. The demand process can also be a factor in employment and workforce within the company. If the demand forecast suggests a very high number, then the company should automatically adjust and makes sure they can comply with the demand and they have enough employees for the huge workload for their upcoming product. They do not really have to hire additional employees full-time but on a project basis only for this high demand product.
from
https://intrepidsourcing.com/extensive-analysis-on-demand-planning-and-forecasting/