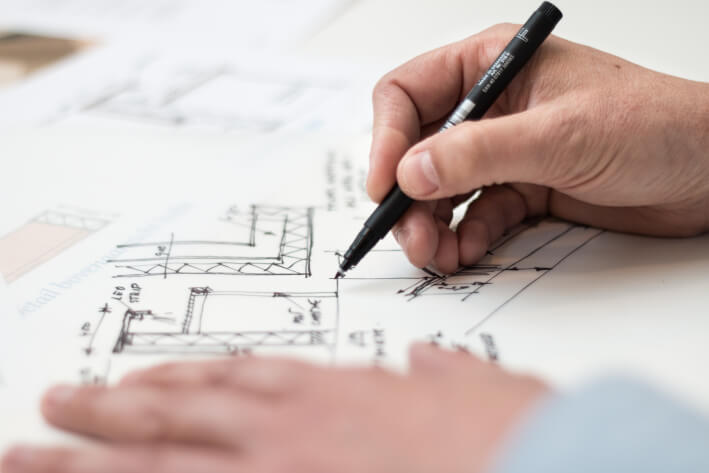
We have already defined production line measures we follow in our company as discussed in the introductory blog series on production line assessment. The company makes sure the suppliers and manufacturers we are working with follow an optimized production process known as “Lean Operations” in the industry. Our intervention in the entire process is limited to show trust to our supplier/manufacturers but we are entirely hands-on when it comes to assessment to make sure we got all aspects of the production line covered.
Sourcing companies and supplier/manufacturers can save lots of time and money with the right production line approach. The efficiency achieved through an enhanced factory production line allows better returns with fewer handovers because of a well-assessed system. Productivity also gets maximized which means more units are produced at the least time required allowing the company to save money from salaries and get the most out of their employees. Production line assessment also detects possible issues to make sure products pass standards during the quality control process.
Production Line Assessment Tools
There are different tools available which help companies conduct production line assessment. Aside from technological equipment, these tools also come as methods and metrics which can enhance the productivity and reliability of the manufacturing production line. The most popular method practiced by OEM companies is Total Productive Maintenance (TPM) as a tool to maintain and improve the production line. This method has derived 2 standardized operations performance metrics: Overall Equipment Effectiveness (OEE) and Overall Resource Effectiveness (ORE). These metrics allow OEM companies to benchmark against competitors in a highly competitive industry.Overall Equipment Effectiveness (OEE)
Overall Equipment Effectiveness (OEE) = Availability (A) x Performance (P) x Quality (Q)
Availability (A) = Actual running time / Planned machine production time
Performance (P) = (Cycle time/unit x Actual Output) / Actual running time
Quality (Q) = (Total Production – Defect) / Total production
OEE helps indicate the difference between the initial and current performance of a system or manufacturing unit. This metric focuses on the performance and productivity of equipment used in the production process ignoring other factors such as labor and material usage.
Overall Resource Effectiveness (ORE)
Overall Resource Effectiveness (ORE) = Readiness (R) x Availability of Facility (Af) x Changeover Efficiency (C) x Availability of Material (Am) x Availability of Manpower (Amp) x Performance (P) x Quality (Q)
Both metrics are proven to be effective to use in measuring a production line. However, the main factor you need to consider in picking a metric to use is to identify the type of losses which affect your production line performance. These losses can vary for production lines even if they are in the same industry.
The Importance of these Metrics as Tools
Measuring the effectiveness of a production line is important so you’d be able to assess all aspects of it. This process will help you determine which part of it needs improvement and which factor is doing you greatly. These metrics as tools will let you maximize your production line to its possible maximum effectivity for the benefit of your clients and company.from
https://intrepidsourcing.com/how-to-measure-the-effectiveness-of-a-manufacturing-production-line/
No comments:
Post a Comment