Product costing is used to make the following products: Garments, Plastics, Electronics, and Branded/Logo Items.
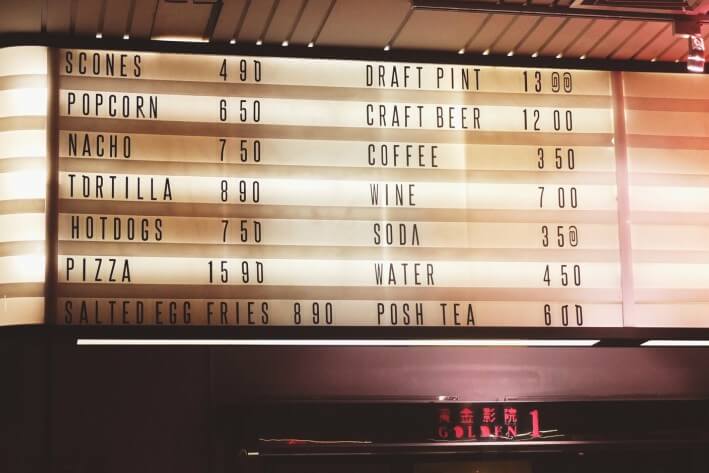
Components of a Product Costing System
This product costing system component must be basic when it comes to calculating product costs since material expenses are where most of the capital goes in terms of production. Material costs also include freight expenses, storage fees, import duties and other expenses directly attributable to material acquisition.Labor Expenses
Factory Overhead
Taxes, Duties, and Fees
Calculating Product Costs
Companies follow different formulas for establishing a product costing system. Here in our company, we follow the standard product costing system in the industry which is to divide the total production cost to the number of units produced. The quotient is the production cost per unit and should be the basis for the actual sales price of the product upon considering other factors such as competition, availability and a lot more. Any amount applied beyond the production cost per unit is already considered as your potential profit and values below the production cost per unit are the loss to the company. This process is how our product costing and pricing is established.For more details specifically about what this service is; click here: Further reading on Cost Estimation.
Click here if you want to set a product costing system for White Label products.
Click here if you want to set a product costing system for Apparel.
Click here if you want to set a product costing system for Electronics.
Click here if you want to set a product costing system for Plastics.
No comments:
Post a Comment