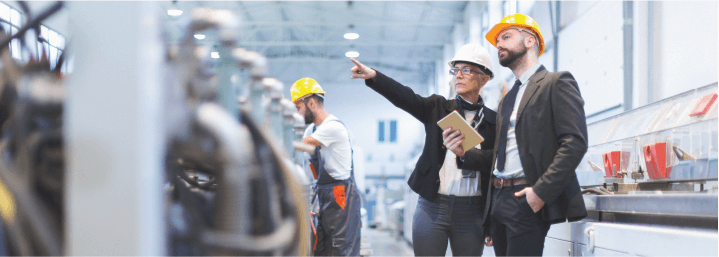
Before you are able to take your product into the market, there are a lot of things to consider such as making sure the product is perfectly designed, has achieved full functionality and looks cool aesthetics-wise. Failure in any of these areas will mean your product has underachieved and is not yet built for the market.
In the world of plastic manufacturing, one of the best ways to approach quality control issues and make sure your plastic product is top notch is doing plastic prototyping. Let us discuss why prototypes for plastic injection molding are essential to the plastic manufacturing business and reveal the simple steps which goes along with the process.
What is Prototype Injection Molding?
Prototype injection molding is a vital process of creating a plastic prototype for a design or concept of a plastic product. The plastic sample serves as a basis for the plastic manufacturers to follow on the production line. This process is essential to assure the product design is up to its specifications and functionality and avoid the loss of money in case you go to full scale production with a flawed design with errors.
Most plastic manufacturers create the design in the computer through a 3D imagery or animation software and eventually create a physical 3D model made out of ABS plastic. This can be done with a 3D print or a soft prototyping mold. The plastic prototype may not be made of the actual material needed for the product design but gives clients and manufacturers a feel for the product design before it goes into actual injection molding or mass production. Corrections can easily be made this way and design flaws will eventually be exposed.
Prototype injection molding is a major step of the quality control process as it oversees product creation and make sure the product is how it is expected to be before it enters mass production. The importance of prototypes for plastic items can’t be overstated and this holds true not only with plastics but in all of manufacturing. Here you can find an article on the meaning and significance.
4 Simple Steps for Making Prototypes for Plastic Items
1. Create a Plastic Product Design
Having a concept or design is always the initial step in manufacturing. Whether you are creating a garment, electronic device or a a packaging product, creating the design and concept should go first and this is no different when it comes to plastic prototyping.
When creating a plastic product design, you should consider feasibility and functionality and make sure the concept is doable. If the design fails the latter then it would be a waste of time and you’d end up creating a design from scratch.
You can collaborate with plastic experts at this stage and do 3D prototyping to make sure your plastic product design can be engineered for production. Knowledge from experts would come in handy and you can easily work altogether as long as you clearly inform them of the concept you have in mind.
2. Product Engineering
At this stage, the plastic product design is ready, has passed functionality standards and all parties have agreed such design is doable in the plastic factory. Production engineering now sets in and we will look for the necessary prototype plastic parts to compose your plastic product. Plastic prototype services are done in a steel tool and the materials must be tapered so they can easily be ejected later on.
The parts should have walls with the right thickness with no undercuts to avoid the steel halves from cracking open or be stuck on one side of the steel tool. We will also determine the gate to which the plastic will be injected and further assess how the plastic material into the gate/s.
As an experienced company who renders plastic prototyping services, we can easily adjust wall thickness to allow the plastic material to flow into the entire gate without overflowing. Factors such as trapped air may be detrimental to the prototype injection molding process, which is why we carefully assess the plastic material and quickly make adjustments before the entire process goes awry.
3. Mold Creation or 3D Printing
For simple and small quantity plastic products, a complex and rather expensive test mold described here is not necessary. Simple 3D printing mentioned earlier is completely sufficient. This is a very simple process that doesn’t need much explanation. A middle ground is making a mold out of special resins that should used if your design is quite complex but you don’t want to spend much money. The process for these molds is the same as for more expensive prototypes for plastic molding.
The actual mold creation is the most critical process in all of plastic prototyping. During this part, the concept and design has already been carefully engineered and it is time to move on to do the actual molds. Prototype injection molding involves the use of plates which will push one part of the mold and water lines are run for the cooling process once the cavities are already filled with the plastic material. For designs with complicated geometrical patterns, the steel tool will require other pieces and not only the two halves of the mold. In contrast to regular injection molds, the steel used is softer and easier to carve out.
Technological advancement have also helped the plastic manufacturing industry through mold flow analysis which digitally simulates the prototype injection molding process to foretell the flow of plastic material into the mold and determine gate locations to locate possible gas traps and plausible areas which cannot be fully filled with the material. KLM, one of our clients, is even experimenting with 3D printing aircraft tools.
4. Taking Advantage of the Injection Mold Machine
Once the mold for the plastic product is created, it will be placed into the injection mold machine and be finally injected with the plastic prototype material. The melted plastic is now injected into the mold while the two halves of the mold are being held together by a clamp through extreme pressure in the form of hydraulics. As the plastic prototype material is being forced into the mold, it will be cooled by the water lines to allow it to solidify. After the cooling process, the pressure from the clamp will now be released and the mold opens up and the plastic design is now materialized.
Conclusion
The process of prototype injection molding follows the same theory for actual production except the former only focuses on coming up with a few prototypes while the latter is designed for mass production. The main idea is to come up with a plastic prototype designed to perfection before you gear up on to high volume production of the design. The prototypes for plastic products gives you time to do modifications and adjust your product instead of wasting money on a substandard plastic product design.
The post 4 Simple Steps to Create Prototypes for Plastic Injection Molds appeared first on Intrepid Sourcing and Services.
from
https://intrepidsourcing.com/trade-wiki/4-simple-steps-to-create-prototypes-for-plastic-injection-molds/
No comments:
Post a Comment